
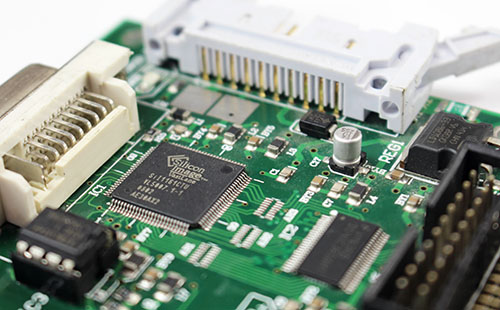
DetaiLED explanation of circuit board manufacturer: conductive hole plug hole process!
For surface mounting plates, especially BGA and IC mounting, the through hole plug hole must be flat, plus or minus 1mil, and there must be no red tin on the edge of the through hole; In order to meet the customer's requirements, the through hole plug hole process can be described as varied, the process flow is particularly long, and it is difficult to control the process. Oil is often lost during hot air leveling and green oil solder resistance test; Oil explosion and other problems occur after curing. According to the actual production conditions, this paper summarizes various PCB plug hole processes, and makes some comparisons and explanations in the process, advantages and disadvantages:
Note: The working principle of hot air leveling is to use hot air to remove the excess solder from the surface and hole of the printed circuit board, and the remaining solder is evenly covered on the bonding pad, barrier free solder lines and surface packaging points, which is one of the methods of surface treatment of the printed circuit board.
1、 Plug hole process after hot air leveling
The process flow is: resistance welding of plate surface → HAL → plug hole → curing. Non plug hole process shall be adopted for production. After hot air leveling, aluminum screen or ink screen shall be used to complete the through hole plug holes of all fortresses required by customers. The hole stopper ink can be photosensitive ink or thermosetting ink. Under the condition that the wet film color is consistent, the hole stopper ink is better to use the same ink as the board surface. This process flow can ensure that the through hole will not lose oil after hot air leveling, but it is easy to cause the ink of the plug hole to pollute the board surface and be uneven. The customer is easy to cause faulty soldering (especially in BGA) during mounting. Therefore, many customers do not accept this method.
2、 Plug hole process before hot air leveling
2.1 Pattern transfer after hole plugging, curing and plate grinding with aluminum sheet
In this process, a numerical control drilling machine is used to drill the aluminum sheet that needs to be plugged, make it into a screen plate, and make the plug hole to ensure that the through hole plug hole is full. The plug hole ink, plug hole ink, or thermosetting ink can also be used. Its characteristics must be high hardness, SMAll resin shrinkage change, and good adhesion with the hole wall. The process flow is: pretreatment → plug hole → plate grinding → pattern transfer → etching → plate surface resistance welding
This method can ensure that the plug hole of the through hole is flat, and the hot air leveling will not have quality problems such as oil explosion and oil loss at the hole edge. However, this process requires one-time thickening of the copper to make the copper thickness of the hole wall meet the customer's standards. Therefore, there are high requirements for the copper plating of the whole plate, and there are also high requirements for the performance of the grinder to ensure that the resin on the copper surface is completely removed, and the copper surface is clean and not polluted. Many PCB plants do not have a one-time copper thickening process, and the performance of the equipment does not meet the requirements, resulting in less use of this process in PCB plants.
2.2 Resistance welding of direct screen plate surface after aluminum sheet plug hole
In this process, a CNC drilling machine is used to drill the aluminum sheet that needs to be plugged into a screen, which is installed on a silk screen machine to plug the hole. After the hole is plugged, the machine shall be parked for no more than 30 minutes. The 36T screen is used to directly screen the surface of the plate for resistance welding. The process flow is: pre-treatment -- plug hole -- silk screen -- pre drying -- exposure -- development -- curing
With this process, it can ensure that the conductive hole cover is well oiled, the plug hole is flat, and the wet film color is consistent. After hot air leveling, it can ensure that the conductive hole is free of tin, and there is no tin bead in the hole, but it is easy to cause the ink pad in the hole after curing, resulting in poor solderability; After the hot air is leveled, the edge of the through hole bubbles and loses oil. It is difficult to control the production with this process method. The process engineer must adopt special processes and parameters to ensure the quality of the plug hole.
2.3 Aluminum sheet plug hole, development, pre curing, plate surface resistance welding after grinding.
Use a numerical control drilling machine to drill the aluminum sheet that requires a plug hole, make it into a screen plate, and install it on the displacement screen printing machine for the plug hole. The plug hole must be full, and the two sides are preferred to protrude. Then, after curing, grind the plate for surface treatment. The process flow is: pre-treatment -- plug hole -- pre drying -- development -- pre curing -- plate surface resistance welding
Because this process uses the plug hole curing to ensure that the oil will not drop or explode after HAL, but after HAL, it is difficult to completely solve the problem of tin coating on the through hole tin bead and through hole, so many customers do not accept it.
2.4 The plate surface resistance welding and plug hole shall be completed at the same time.
This method uses 36T (43T) screen, which is installed on the screen printing machine, and uses a backing plate or a nail bed. While completing the board surface, all the through holes are plugged. The process flow is: pretreatment -- screen printing -- pre drying -- exposure -- development -- curing.
This process has a short time and a high utilization rate of equipment, which can ensure that no oil will fall from the vias and no tin will be added to the through holes after hot air leveling. However, due to the use of silk screen to plug holes, there is a large amount of air in the vias. When curing, the air expands and breaks through the solder mask, causing holes and irregularities. A small amount of tin will be hidden in the through holes after hot air leveling. PCB manufacturers, PCB designers and PCBA processors will explain the process of conductive hole plug hole.
然后
聯系
電話熱線
13410863085Q Q
微信
- 郵箱