
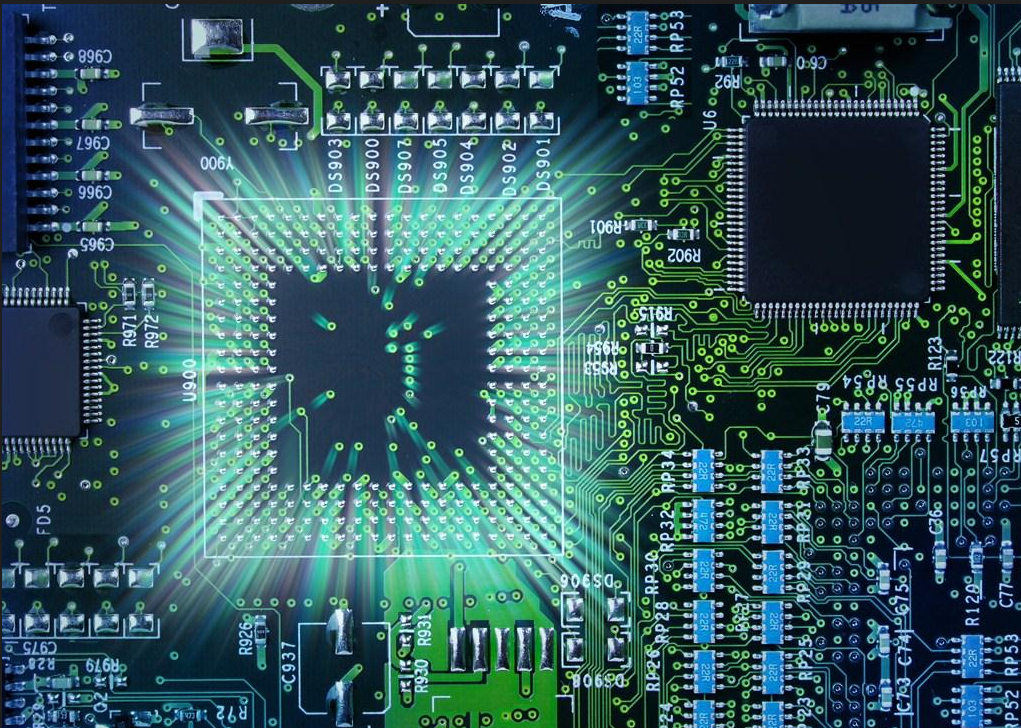
Possible PCB quality problems in PCB manufacturing
PCB quality problems PCB manufacturing mainly includes the following points:
1、 Various welding problems
Symptoms: There are blasting holes at cold welding or tin welding points.
Reflection method: analyze the hole before and after immersion and welding to find out the stress center of copper. In addition, raw materials shall be subject to incoming inspection.
reason:
1. Porosity or cold spot occurs after welding. In many cases, the copper plating is poor and then shrinks during the welding operation, resulting in holes or bursting holes in the wall of the metallized hole. If this happens during wet processing, the absorbed volatilization
The material is covered with coating and then discharged under the heating of immersion welding, whICh will result in nozzle or bursting hole.
Handling method:
1. Try to eliminate copper stress. Shrinkage of laminates in the z-axis or thickness direction is usually related to data. It can promote the fracture of metallized holes. Work with laminate manufacturers to obtain recommendations for information on SMAll z-axis shrinkage.
Printed circuit board
2、 Bond strength problem
Symptom: The pad is separated from the conductor during immersion welding.
IntrOSPective method: During the incoming inspection, stop adequate testing and carefully control all wet processing processes.
Cause:
Solder pads or wires falling off during processing may be caused by electroplating solutions, solvent etching, or copper stress during electroplating operations.
2. Punching, drilling, or piercing will partially separate the liner and become clear during hole metallization operations.
3. During wave soldering or manual soldering, the separation of pads or wires is usually caused by improper welding process or excessive temperature transition. SometiMES, due to poor adhesion of the laminate or low thermal peeling strength, a gasket or wire separation will be formed.
4. The design and wiring of PCB multilayer boards sometimes lead to the separation of pads or wires in the opposite center.
5. During the welding operation, the residual heat absorbed by the component will cause the bonding pad to separate.
Handling method:
1. Provide the laminate manufacturer with a complete list of solvents and solutions used, including processing time and temperature for each step. Analyze whether copper stress and excessive thermal shock occur during electroplating.
2. Strictly follow the pushing processing method. The analysis of metallized holes can control this result.
3. Because the requirements for all operators are not strict, most pads or wires are separated. It will also disengage when the bath temperature detection takes effect or the dwell time in the bath is extended. In the manual tin cutting operation, the pad separation is probably caused by improper use of watt
Electric ferrochrome and failure to stop professional process training. Today, some laminate manufacturers have produced laminates with high peel strength at low temperatures for severe welding applications.
4. If the separation caused by the design wiring of the printed board occurs in the relative center of each board; The printed board must then be redesigned. Usually, this happens in the right angle center of thick copper foil or copper wire. Sometimes, there will be such scenes in the long run; This is because
Because the thermal shrinkage coefficient is different.
5. If possible, remove heavy components from the whole PCB or install them after immersion welding. Usually, low wattage electric soldering iron is used for careful soldering. The continuous heating time of substrate data is shorter than that of element immersion welding.
Printed circuit board
3. Excessive size change
Symptom: After processing or welding, the dimension of the base plate exceeds the tolerance or cannot be aligned.
Reflection method: completely stop the quality control during the processing.
reason:
1. The structure texture direction of the paper-based data is not noticed, and the positive shrinkage is about half of the horizontal direction. In addition, the substrate cannot be restored to its original size after cooling.
2. If some of the stresses in the laminate are not released, irregular dimensional changes may sometimes occur during processing.
Handling method:
1. Instruct all consumers to cut plates in the opposite direction to the structure and texture. If the size change exceeds the allowable range, the base material can be used.
2. Contact the laminate manufacturer to find out how to release data stress before machining.
然后
聯系
電話熱線
13410863085Q Q
微信
- 郵箱