
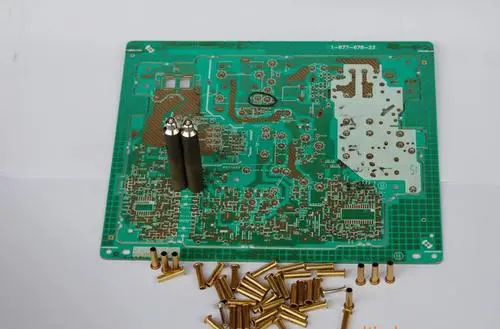
硫酸銅電鍍在PCB電鍍中起著極其重要的作用。 酸性電鍍銅的質量直接影響鍍銅層的質量和相關的機械性能,并對后續(xù)加工產生一定的影響。 因此,如何控制酸性銅電鍍的質量是PCB電鍍的重要環(huán)節(jié),也是很多大廠難以控制的工序之一。 筆者根據(jù)多年從事電鍍和技術服務的經驗,初步總結如下,希望對PCB行業(yè)的電鍍經營者有所啟發(fā)。 硫酸銅電鍍常見問題主要有以下幾點:
粗電鍍;
電鍍(板面)銅粒;
電鍍坑;
板面發(fā)白或顏色不均。
針對以上問題,作了一些總結,并進行了一些簡要分析、解決措施和預防措施。
粗電鍍:
一般板角粗糙,多半是電鍍電流大造成的。 可以降低電流,用卡表檢查電流顯示是否異常; 整板粗糙,一般不會出現(xiàn),但筆者曾與客戶會面過一次,后來發(fā)現(xiàn)是冬天氣溫低,打磨的內容不夠; 另外,有時一些返工掉膜板表面沒有清理干凈。
電鍍板上的銅粒:
造成板面銅粒的因素有很多。 在沉積銅和圖案轉移的整個過程中,可以在PCB上電鍍銅。 筆者曾在國營大廠遇到過因沉銅造成的板子上的銅粒。
1、析銅工藝造成的板面銅粒,可能是任何析銅工藝步驟造成的。
1.堿性除油不僅會造成板面粗糙,而且在水硬度高、鉆塵過多(特別是雙面板過濾不當?shù)那闆r下)時,也會造成孔內粗糙,但 一般只會造成孔內粗糙,板面輕微的點蝕污垢和微腐蝕也可以去除。
2.微蝕主要有以下幾種情況:
用作微蝕劑的雙氧水或硫酸質量太差,或過硫酸銨(過硫酸鈉)雜質過多。 一般建議至少要CP級。 此外,工業(yè)級會造成其他質量故障; 微蝕槽內含銅量過高或溫度過低,造成硫酸銅晶體析出緩慢; 槽液渾濁污染:a 活化液多為污染或維護不當造成,如過濾泵漏氣、槽液比重低、含銅量高(活化槽已使用過 很長一段時間,超過 3 年)。 這樣,槽液中就會產生粒狀懸浮物或雜質膠體,吸附在板面或孔壁上,并伴有孔內粗糙。 b. 脫膠或加速:槽液使用時間過長,出現(xiàn)渾濁,因為現(xiàn)在的溶液大多是用氟硼酸配制的,氟硼酸會侵蝕FR-4中的玻璃纖維,導致槽液中的硅酸鹽和鈣鹽增多 罐解決方案。 另外,槽液中銅含量的增加和錫的溶解都會導致板面銅粒的產生。
3.銅沉降槽本身主要是由于槽液活性過高,空氣攪動灰塵,槽液中懸浮有許多小顆粒造成的。 可通過調整工藝參數(shù)、增加或更換空氣濾芯、全罐過濾等方法有效解決。
4.沉銅后,銅板稀酸槽應暫存,并保持槽液清潔。 如果槽液渾濁,應及時更換。
5.銅板存放時間不宜過長,否則板面容易氧化,即使在酸溶液中,氧化后氧化膜也較難去除,因此板面也會產生銅 粒子。
除了上面提到的沉銅工藝沉積的銅粒外,它們一般均勻分布在板面,規(guī)律性強,這里產生的污染,無論導電與否,都會導致鍍銅板上的銅粒 印刷電路板。 可用一些小試板逐級單獨加工,進行比較判斷,現(xiàn)場故障板可用軟刷解決。
2、圖文轉印工藝:顯影有殘膠(極薄殘膜也可在電鍍時鍍覆),或顯影后未清洗版材,或圖文轉印后版材放置時間過長, 導致板材表面不同程度的氧化,尤其是板材清洗不當或倉儲車間空氣污染較重時。 解決辦法是加強水洗,加強計劃調度,加強酸洗強度。
3、此時酸性銅電鍍液本身的預處理一般不會造成板子上有銅粒,因為不導電的粒子極有可能造成板子漏鍍或麻點。
4、銅缸引起板面銅粒的原因可歸納為:槽液參數(shù)的維護、PCB生產操作、材料及PCB工藝維護:槽液參數(shù)的維護包括硫酸含量過高、太高等。 銅含量低,槽液溫度過低或過高,尤其是在沒有溫控冷卻系統(tǒng)的PCB廠,會導致槽液的電流密度范圍下降。 按正常生產流程操作,槽液中可能會產生銅粉混入槽液; 在生產操作上,電流過大、夾板不良、夾點空、槽內靠陽極溶解掉板等也會造成部分板電流過大,產生銅粉,落入槽液,逐漸 產生銅粒斷層; 材料方面,主要問題是磷銅中角磷的含量和磷分布的均勻性; 在生產和維護方面,主要是大處理。 添加銅角時,它們會掉入槽中。 主要是大處理、陽極清洗和陽極袋清洗。 很多工廠處理不好,存在一些隱患。 銅球的主要處理方法是將表面清洗干凈,用雙氧水對新銅表面進行輕微腐蝕。 陽極袋依次用硫酸雙氧水和堿性溶液浸泡,清洗干凈。 特別是陽極袋要使用5-10微米縫隙的PP濾袋。
然后
聯(lián)系
電話熱線
13410863085Q Q
微信
- 郵箱