
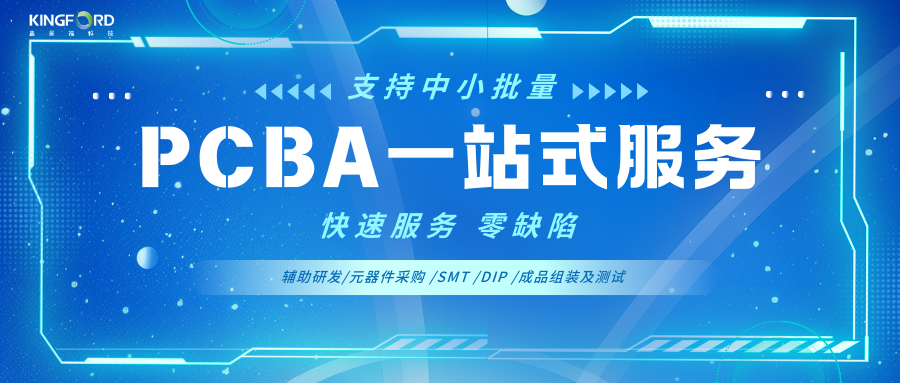
在PCBA制造行業,產品質量直接決定了電子設備的可靠性和市場競爭力。然而,行業普遍面臨諸多痛點:設計缺陷導致生產不良率高、供應鏈不穩定導致來料品質差、生產過程管控不足引發批量性報廢、售后問題無法快速響應等。這些問題不僅影響交付周期,更可能損害客戶信任。
鑫景福作為一家深耕PCBA制造13年的企業,通過嚴格的19道質檢工序,實現了99.9%的直通率,在行業中樹立了標桿。本文將從PCBA行業的痛點出發,解析這19道質檢工序如何層層把關,確保產品零缺陷交付。
為什么PCBA制造需要極致的質檢體系?
在PCBA制造過程中,常見的問題包括:
1. 設計與生產脫節:部分客戶的設計未考慮可制造性(DFM),導致生產時不良率高,需多次返工。
2. 供應鏈風險:元器件供應商良莠不齊,假貨、翻新件可能導致整批產品失效。
3. 生產過程失控:焊錫不良、元器件貼裝偏移、虛焊等問題頻發,影響功能穩定性。
4. 售后響應滯后:出現質量問題后,部分廠商缺乏快速分析能力,導致交付延遲。
這些痛點直接影響客戶的滿意度,甚至可能引發批量性報廢,造成巨大損失。因此,一套科學、嚴格的質檢體系,成為PCBA工廠的核心競爭力。
19道質檢工序如何實現99.9%直通率?
鑫景福的質檢體系覆蓋研發、來料、制程、功能測試、終檢五大階段,確保每個環節的可控性。
1. 研發階段:提前規避設計缺陷
● DFM可制造性分析:利用專業軟件對客戶的設計文件進行仿真測試,識別潛在工藝風險,如焊盤間距過小、元件布局不合理等。
●失效模式分析(FMEA):預測生產過程中可能出現的失效點,提前優化工藝參數。
2. 來料檢驗:嚴控元器件質量
●供應商資質審核:只與原廠或一級代理商合作,確保物料來源可靠。
●X-RAY檢測 & 開蓋測試:針對高端芯片、BGA封裝器件,采用X光透視+開蓋檢測,杜絕假貨、翻新料。
● RoHS & REACH環保檢測:確保所有物料符合國際環保標準。
3. 生產過程:全自動化+實時監控
●3D SPI錫膏檢測:在貼片前檢查錫膏印刷厚度、面積,避免虛焊或橋接。
● AOI自動光學檢測:高速攝像頭掃描每一塊PCBA,精準識別元件漏貼、偏移、極性錯誤等缺陷。
● X-RAY檢測BGA焊接:對隱藏焊點進行無損探傷,確保焊接可靠性。
● 首件檢驗(雙重復核):由品質工程師+電子工程師雙重確認首件樣品,確保工藝參數正確。
4. 功能測試:模擬真實使用環境
●FCT(功能測試):自主開發測試軟件,驗證PCBA的電壓、電流、通信等功能,覆蓋率超80%。
●高溫老化測試:模擬長期運行環境,篩選潛在早期失效產品。
5. 終檢 & 出貨:100%全檢
● 三防漆涂覆檢測:確保防潮、防腐蝕涂層均勻無遺漏。
● AQL抽檢 & OQC終檢:按國際抽樣標準(如MIL-STD-105E)進行最終把關,確保整批產品合格率。
為什么鑫景福能做到99.9%直通率?
1. 先進的檢測設備:采用雅馬哈貼片機、3D SPI、X-RAY等高端設備,減少人為誤差。
2. 嚴格的供應鏈管理:與300+原廠供應商合作,避免來料問題。
3. 數字化管控:MES系統實時監控生產數據,問題可追溯至具體批次、工位。
4. 資深團隊:品質總監擁有15年經驗,精通APQP、PPAP等汽車行業質量管理工具。
結語:零缺陷不是口號,而是系統化工程
在PCBA行業,99.9%的直通率并非偶然,而是從設計到交付的全流程精準管控的結果。鑫景福通過19道質檢工序,不僅解決了行業痛點,更成為汽車、醫療設備廠商等高端客戶的長期合作伙伴。
未來,隨著智能制造的發展,AI質檢、大數據預測分析將進一步推動PCBA質量升級。而核心始終不變:只有每一道工序都極致嚴格,才能真正實現“零缺陷”交付。
然后
聯系
電話熱線
13410863085Q Q
微信
- 郵箱