
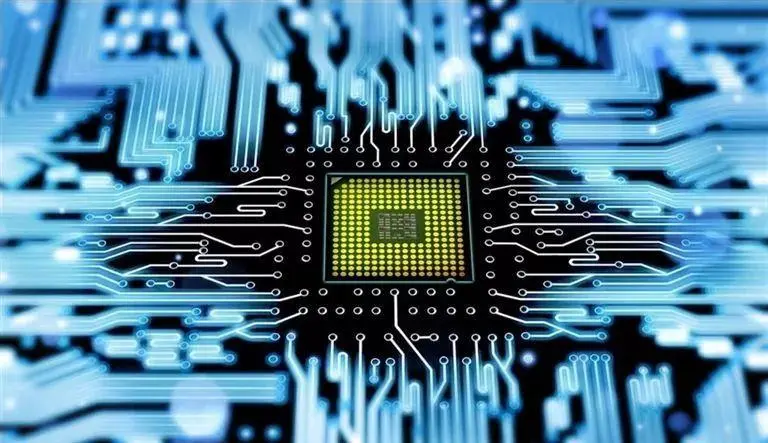
大凹坑通常表明油被污染。 如果混合不好,氣泡就無法排出,從而形成凹坑。 可以使用潤濕劑來減少其影響。 我們通常稱小凹坑為針孔。 預處理不當、金屬雜質過少、硼酸含量過低以及鍍液溫度過低都會產生針孔。 鍍液維護和PCB工藝控制是關鍵,應使用防針孔劑作為PCB工藝穩定劑來補充。
印刷電路板
粗糙和毛刺:粗糙意味著溶液較臟,可以通過適當的過濾來糾正(如果pH值太高,應控制氫氧化物的沉淀)。 如果PCB電流密度過高,陽極泥和補充水中的雜質會帶入雜質,嚴重時會造成粗糙和毛刺。
附著力低:PCB銅鍍層若未完全脫氧,鍍層會剝落,銅與鎳之間的附著力較差。 如果電流中斷,中斷時會導致鎳鍍層剝落,溫度過低時也會剝落。
鍍層易碎、可焊性差:當印制PCB的鍍層彎曲或磨損到一定程度時,通常表明鍍層已脆。 這表明存在有機或重金屬污染,過量的添加劑、夾帶的有機物和電鍍緩蝕劑是有機污染的主要來源,必須用活性炭進行處理。 添加劑不足和pH值過高也會影響涂料的脆性。
電鍍顏色深、顏色不均勻:電鍍顏色深、顏色不均勻,表明有金屬污染。 由于通常先鍍銅,再鍍鎳,引入的銅液是主要污染源。 盡量減少吊架上的銅溶液非常重要。 為了去除槽內的金屬污染物,特別是除銅液,應采用波紋鋼陰極。 以 2 至 5 A/平方英寸的電流密度電鍍每加侖溶液 5 安培 1 小時。 預處理不良、電鍍不良、電流密度低、主鹽濃度低、電鍍電源電路接觸不良等都會影響電鍍顏色。
涂層燒傷:PCB涂層燒傷的可能原因:硼酸不足、金屬鹽濃度低、工作溫度低、電流密度高、pH值高或攪拌不足。
沉積速率低:pH值低或電流密度低會導致沉積速率低。
鍍層起泡或剝落:PCB電鍍前預處理不良、中間斷電時間過長、有機雜質污染、電流密度過高、溫度過低、pH過高或過低、雜質影響嚴重都會導致起泡或剝落。 脫皮。
然后
聯系
電話熱線
13410863085Q Q
微信
- 郵箱